Fourth, processing cases
Jet engine combustion chamber
Material: Inconel 718 forged blank Hardness: 35HRC Surface: pre-machined Process: semi-finishing Material grade: CBN10 Blade model: TNGN110308E25-L1 Cutting speed: 350m/min Feed rate: 0.25mm/rev Cutting depth: 0.5mm Coolant: Yes Result CBN10=Processing time: 6 minutes Whisker toughened ceramic = 10 minutes | 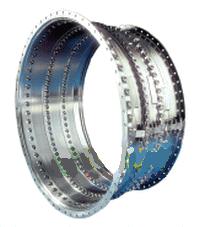
| 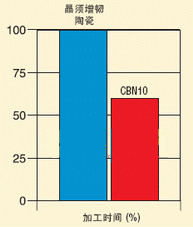
|
External turning of the shaft
Material: Inconel 718 forged blank Surface: pre-machined Process: semi-finishing Material grade: CBN10 Blade model: TNGA160408E25-L1 Cutting speed: 300m/min Feed rate: 0.10mm/rev Cutting depth: 0.5mm Coolant: Yes Result Tool life: 12 minutes | 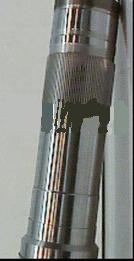
| 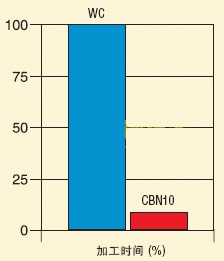
|
Shaft of the shaft
Material: Inconel 718 forged blank Hardness: 35HRC
Material grade / blade: CBN10=LCGN1604M0-0400E25-LF
WC=LCMR1604M0-0400-MP,883 Cutting speed: CBN10=170m/min
WC=30m/min Feed amount: CBN10/WC=0.2mm/rev
Cutting depth: CBN10/WC=0.2mm Coolant: Yes
result Tool life: CBN10=12 minutes
WC=10 minutes CBN10 reduces cutting time by up to 85% and improves surface roughness
V. Conclusion In general, Inconel 718 is a difficult material to process, and the machining parameters need to be optimized for each part to maximize tool life. The micro-cracking of the cutting edge, rapid wear of the flank and groove wear are the most common problems in processing this material. Cutting edge grinding has a significant impact on tool life. Care should be taken when attempting to exceed the recommended depth of cut.
Previous page
Disposable Surgical Clothes
Medical Coveralls,Surgical Coverall,Disposable Surgical Clothes,Medical Protective Clothing
Ningbo Autrends Prevention Products Co., Ltd , https://www.autrendsafety.com